Производство тентовых конструкций осуществляется на собственном производстве под строгим контролем качества, что позволяет обеспечивать полное соответствие продукции проектной документации. Общая площадь производственных мощностей нашего предприятия составляет более 2000 м2.
ИЗГОТОВЛЕНИЕ ТЕНТОВЫХ ПОКРЫТИЙ
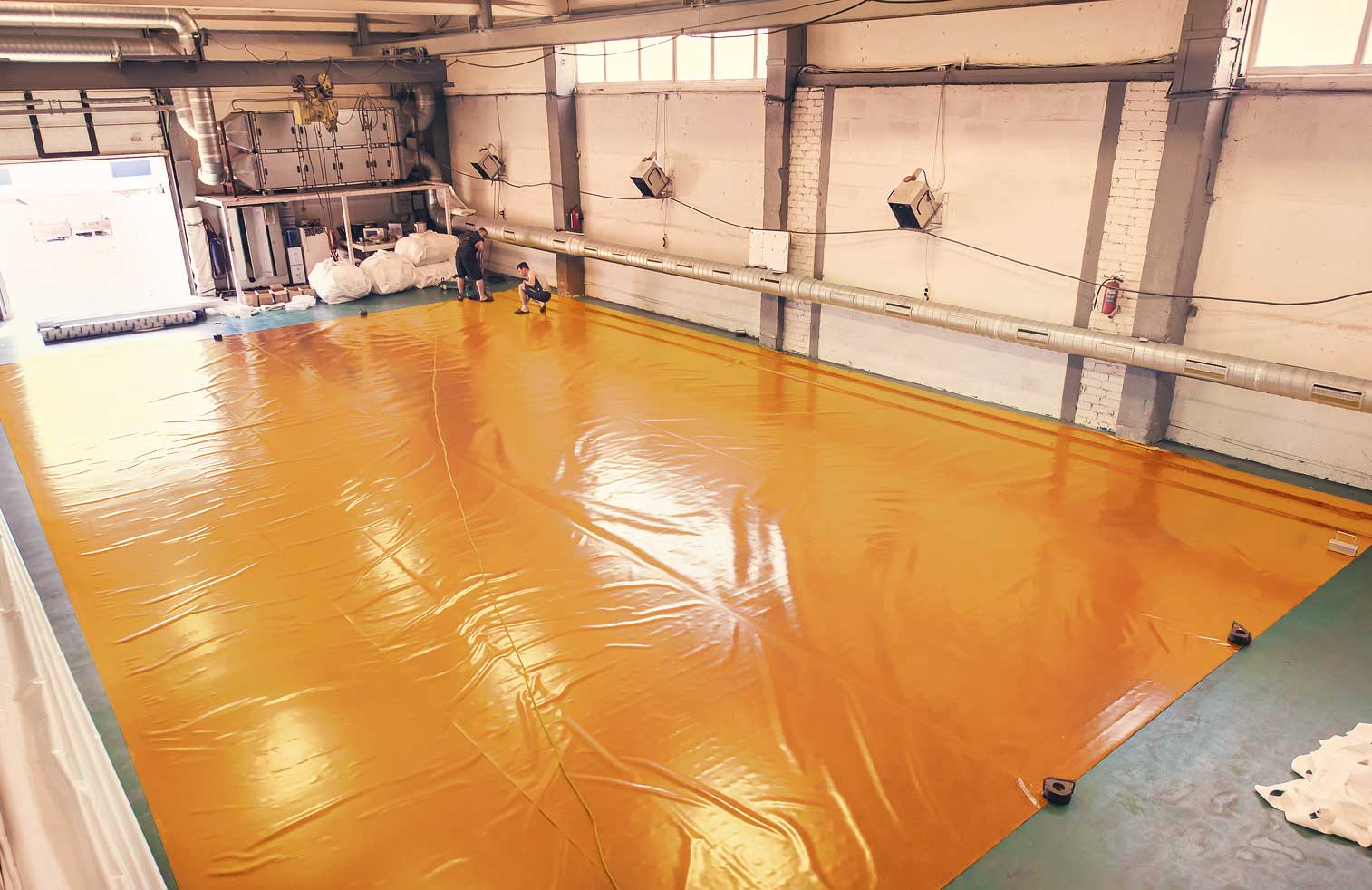
Участок раскроя и сварки тентовых покрытий (мембран):
Полезная площадь участка более 500 м2, что позволяет изготавливать крупные секции тентового покрытия для сооружений больших размеров. Применение современного автоматизированного оборудования позволяет изготовить с высокой точностью любые покрытия сложной геометрической формы.
Сварка тентов производится на надежном и качественном оборудовании фирмы Ляйстер (Швейцария). Использование данного оборудования обеспечивает в процессе сварки повышенную герметичность, пыленепроницаемость и долговечность изделия в местах сварных швов.
ИЗГОТОВЛЕНИЕ МЕТАЛЛОКОНСТРУКЦИЙ
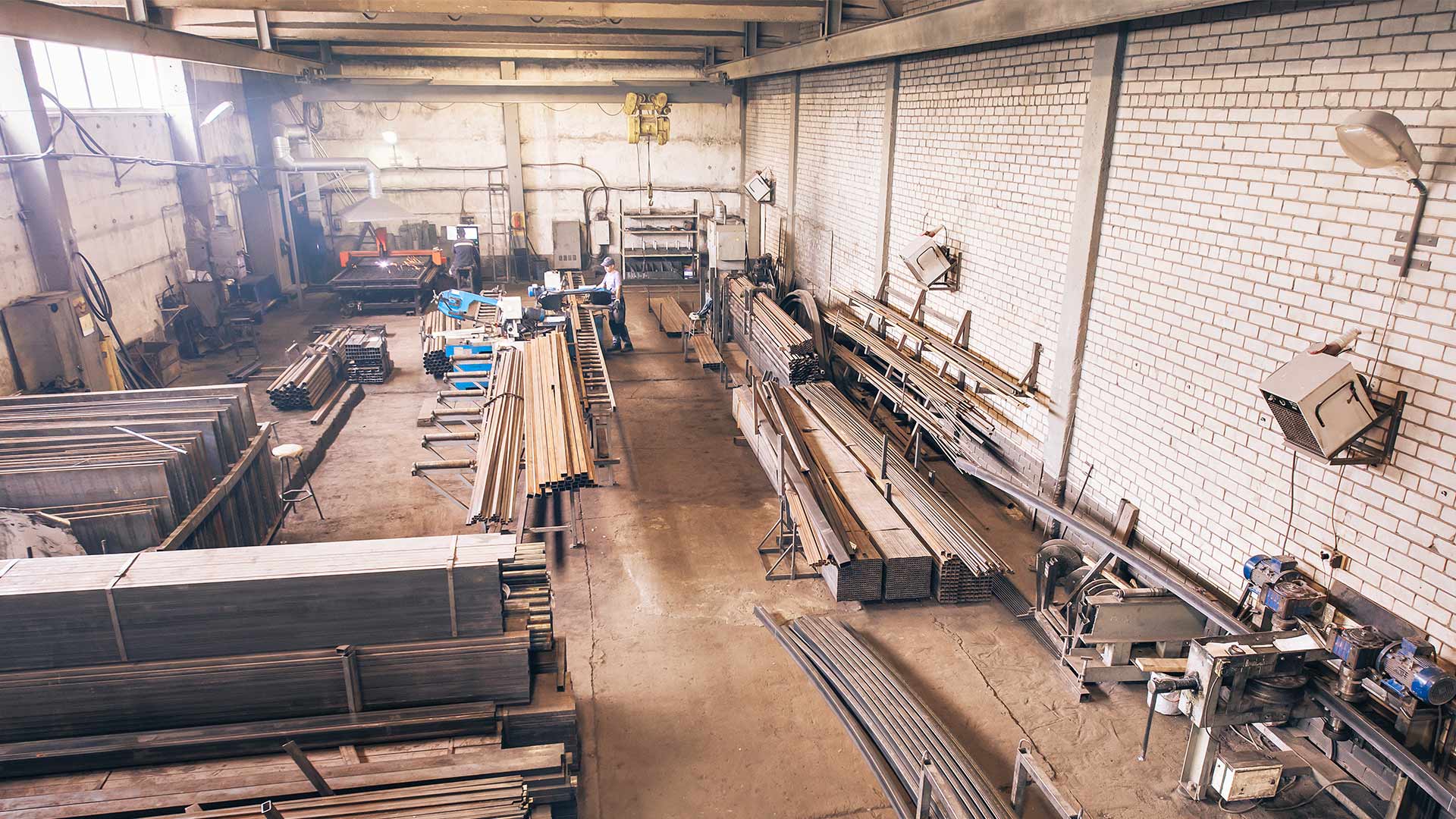
Участок заготовки металлоконструкций:
Участок оснащен современным оборудованием, необходимым для резки, рубки и другой заготовительной работы. Состав оборудования:
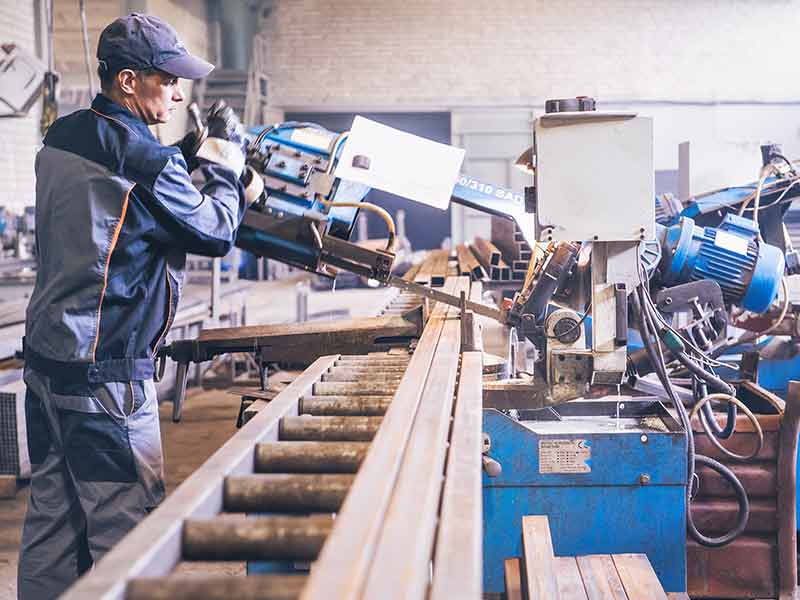
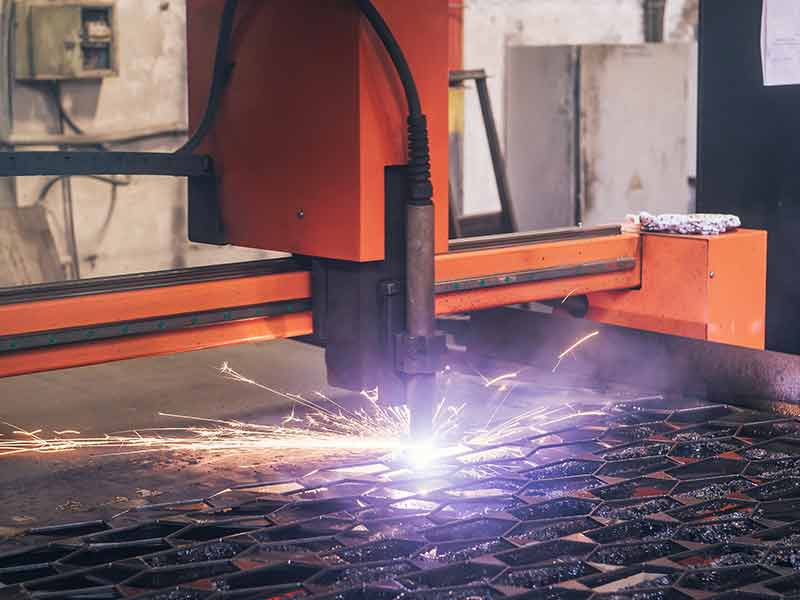
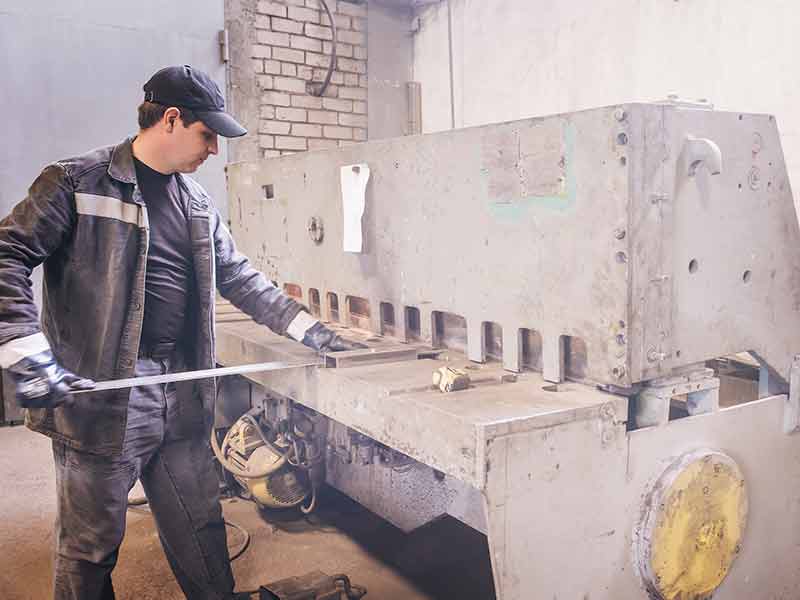
- – Ленточнопильные станки (Чехия)
- – Установка плазменной резки с ЧПУ (США)
- – Гильотина
Участок механической обработки:
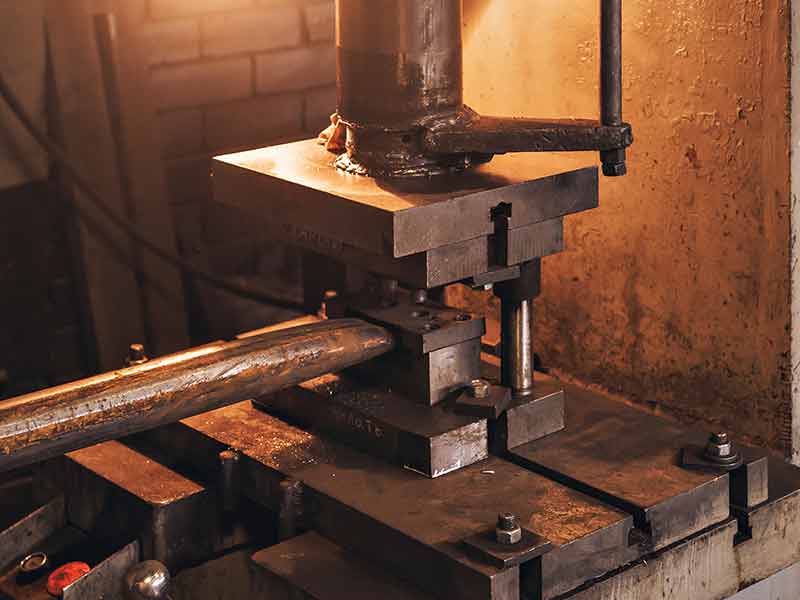
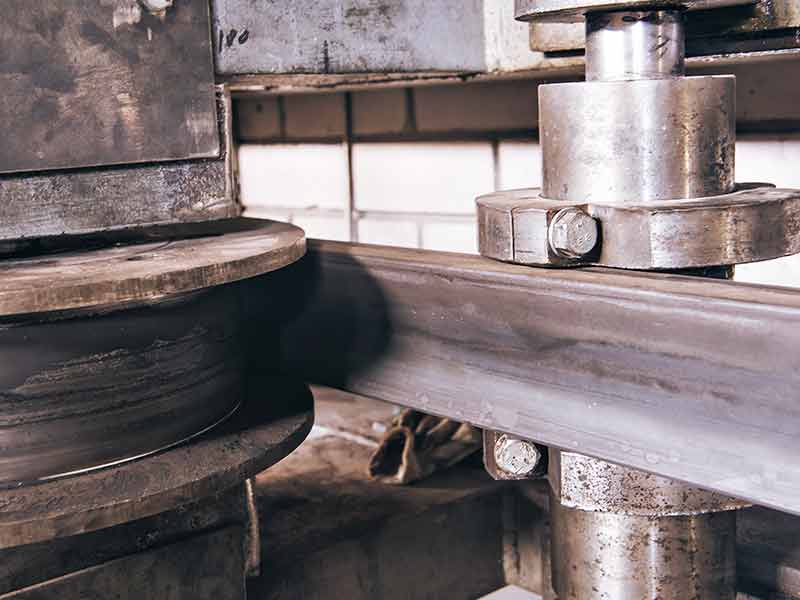
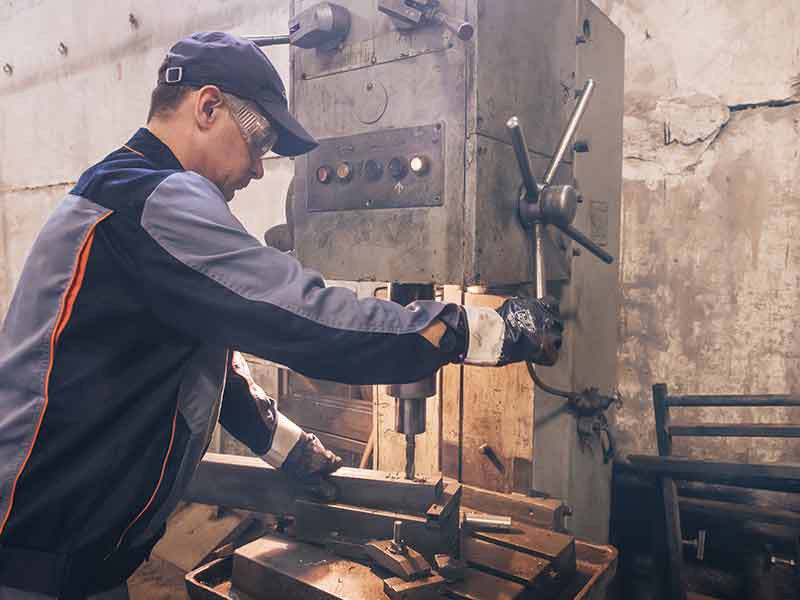
- – Пресс гидравлический
- – 3-роликовый профилегибочный станок
- – Сверлильные станки
Участок сварки металлоконструкций:
- – Сборка металлоконструкций под сварку осуществляется на координатных столах с использованием кондукторов.
- – Сварка металлоконструкций осуществляется полуавтоматическим способом по ГОСТ 14771 в среде защитных газов.
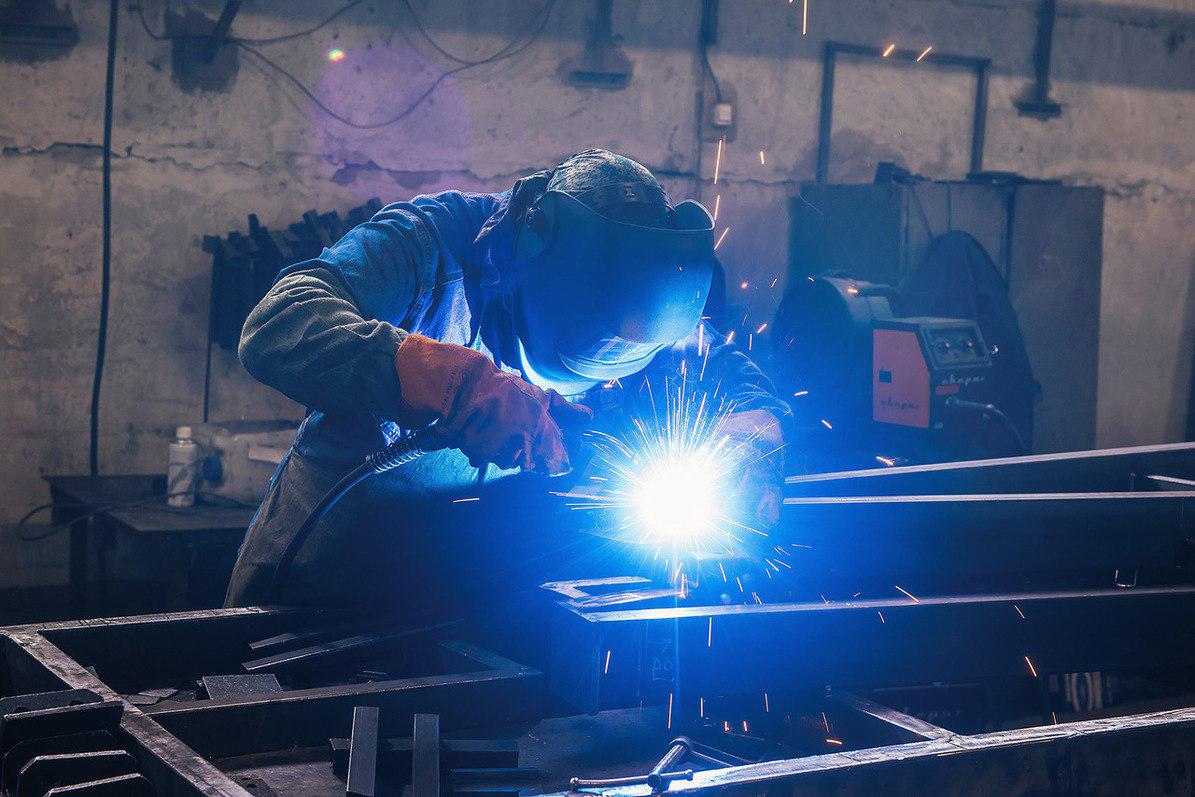
Защита металлокаркаса от коррозии:
Производственная компания «ТЕНТПРО» внедрила современную технологию порошково-полимерной окраски металлоконструкций, которой в настоящее время практически нет аналогов по качеству и долговечности. Данная технология позволяет получать высококачественные покрытия с хорошей антикоррозийной стойкостью, сравнимую с горячим цинкованием, высокой ударопрочностью и отличным внешним видом. Расчетный срок эксплуатации металлокаркаса ангаров до ремонта — 25 лет. Столь значительный срок обеспечивается современными технологиями нанесения антикоррозийного покрытие и использованием порошковых красок от лучших европейских производителей.
Порошковые цинкнаполненные полиэфирные краски "Teknos" (Финляндия), благодаря высокому содержанию цинка, кроме протекторной защиты обеспечивает и катодную защиту стали. В местах дефектов в покрытии цинк предотвращает распространение подпленочной коррозии.
Применение цинксодержащей краски на изделиях, применяемых в тяжелых климатических условиях, позволяет увеличить срок их службы в 5-7 раз. Это особенно важно в ответственных изделиях, демонтаж и замена которых связана с большими трудностями и затратами.
Преимущества порошковой окраски:
- – Стойкость к воздействию химикатов, бензина, солестойкость и устойчивость к УФ облучению.
- – Отличная устойчивость к абразивному истиранию и ударопрочность.
- – Стойкость к температурным перепадам.
- – Надежная защита скрытых углов и кромок.
- – Высокая адгезия (сцепление покрытия с поверхностью).
- – Отсутствие подтеков на вертикальных поверхностях.
- – Повышенная прочность на удар, изгиб.
- – Экологичность: отсутствие огнеопасных и токсичных растворителей в значительной мере решает проблему охраны окружающей среды и техники безопасности.
Современная порошковая краска — это многокомпонентный твердый состав, который под воздействием высокой температуры образует на покрытии тонкую, сплошную пленку. С теоретической точки зрения, порошковая краска является полимером, а потому ее нередко называют «полимерная краска» или «полимерное покрытие».
Отличительной чертой порошковых красок от традиционных жидких ЛКМ является то, что они не содержат органических и других летучих веществ. В настоящее время порошковым краскам практически нет аналогов среди ЛКМ, которые позволяли бы применять безотходную технологию покраски покрытий. Помимо многочисленных преимуществ при нанесении и использовании - данный тип красок позволяет получать высококачественные покрытия с хорошей антикоррозийной стойкостью, высокой ударопрочностью и, как правило, без предварительного грунтования. Полный производственный цикл (обезжиривание, фосфатирование, промывка, сушка), обеспечивает образование ударопрочного антикоррозийного покрытия, которое работает в температурном диапазоне от -60 до + 150°С и обеспечивает надежную электроизоляцию.
Технологический процесс:
Типовой технологический процесс получения покрытий из порошковых красок включает три основные стадии: подготовку поверхности, нанесение порошкового материала, формирование из него покрытия (запекание). Качество покрытий зависит от строгого соблюдения технологических режимов всех стадий процесса.
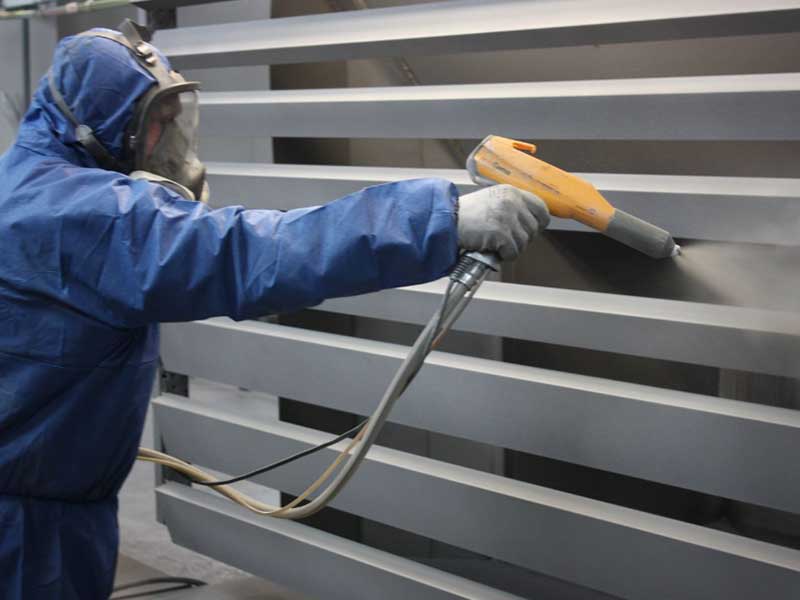
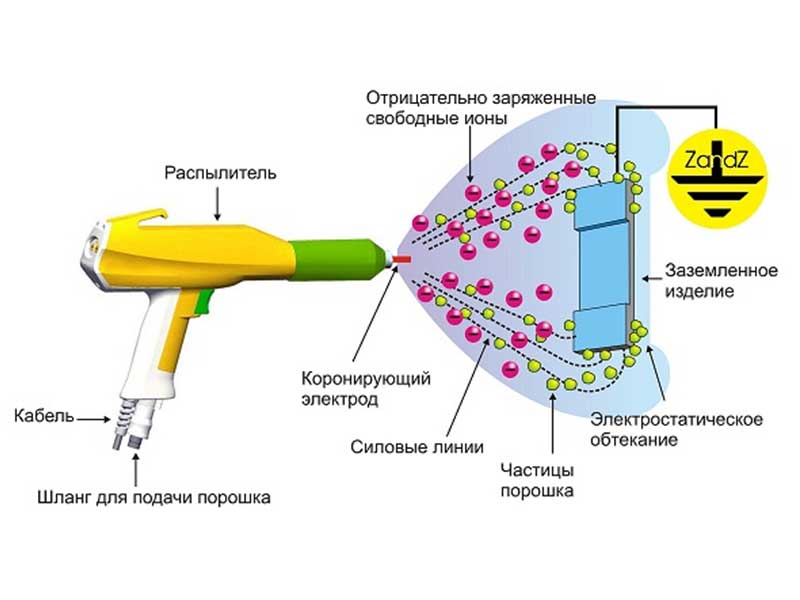
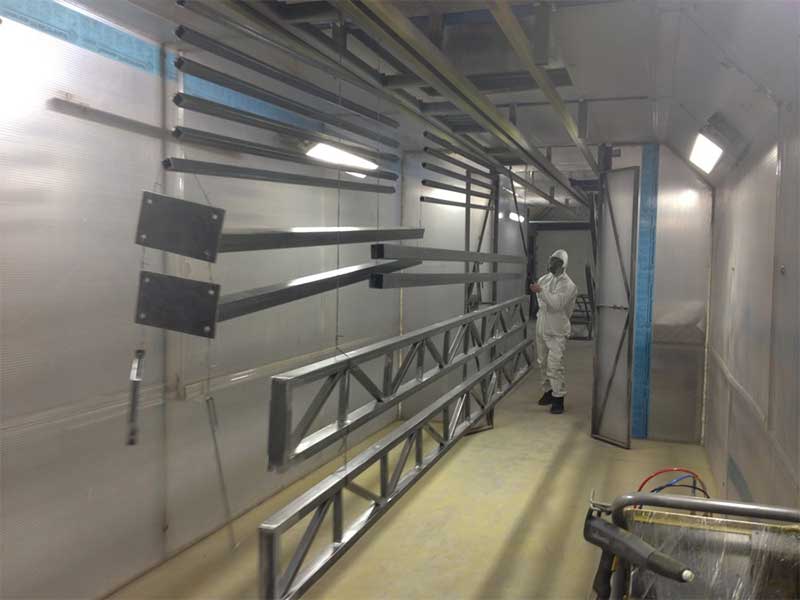
Подготовка поверхности изделия к порошковой покраске:
Очистка, обезжиривание, фосфатирование, сушка. Подготовка поверхности в значительной степени определяет качество покраски, внешний вид, коррозионную стойкость, долговечность.
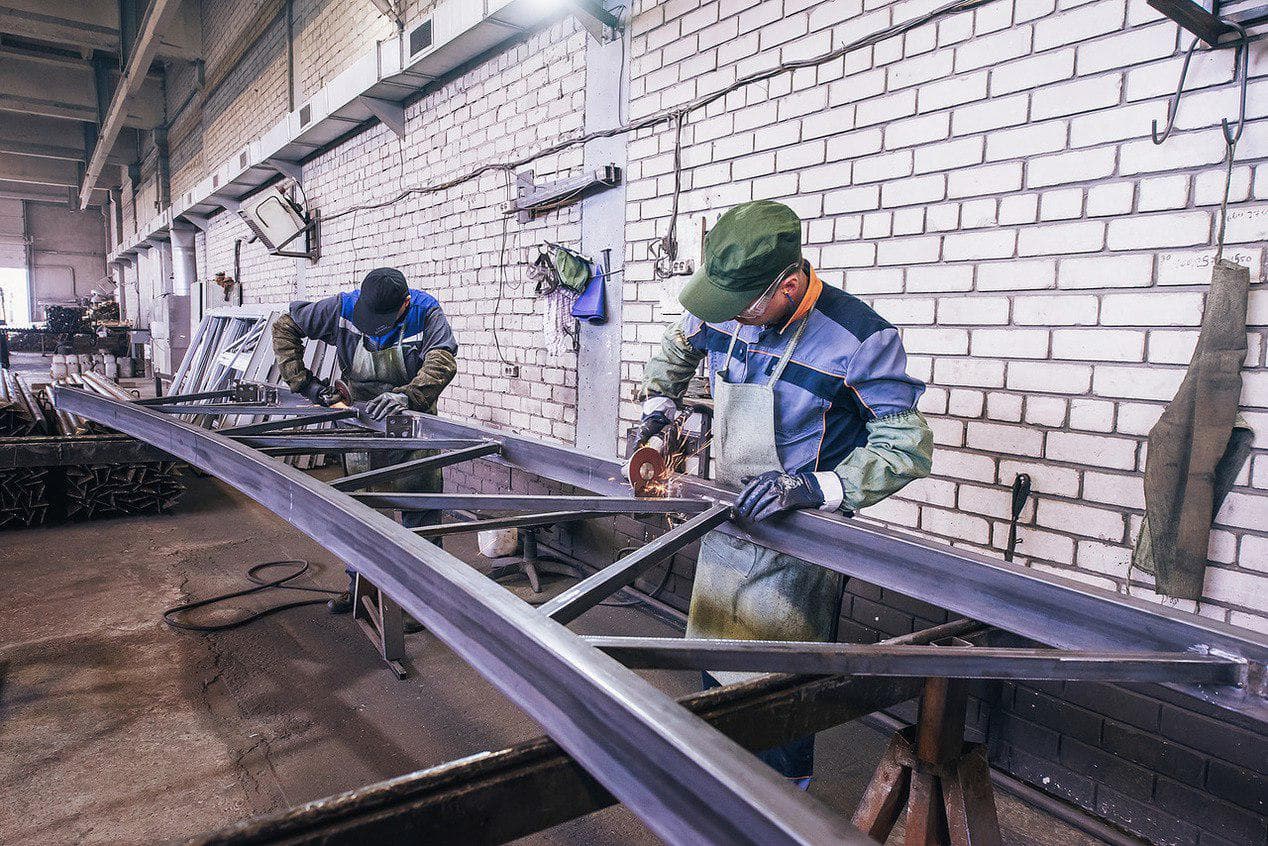
Нанесение:
Нанесение на окрашиваемую поверхность порошкового покрытия происходит в камере напыления с помощью пистолета-распылителя, в котором частицам полимерного порошка придаётся электрический заряд и который с помощью сжатого воздуха транспортирует порошок к детали. Под воздействием электростатических сил частицы порошка притягиваются к поверхности окрашиваемой детали и равномерными слоями располагаются на ней. Не осевшие на изделие частицы порошковой краски улавливаются в окрасочной камере и могут быть использованы для повторного напыления, что невозможно при использовании обычных жидких красок. Далее изделие с нанесенной порошковой краской переносится в камеру полимеризации для отверждения краски.
Полимеризация:
Для отверждения порошковой краски используются печи полимеризации. Печь полимеризации — закрытая камера, внутренний рабочий объем которой нагревается до необходимой для полимеризации температуры. Окрашиваемое изделие помещается внутрь камеры, где и происходит полимеризация порошкового покрытия. Оплавление и полимеризация происходит при температуре 150-220 °С в течение 15-30 минут, после чего изделие охлаждается на воздухе. После остывания изделия покрытие готово. В результате получается долговечное, стойкое, высококачественное и привлекательное на вид покрытие с отличными защитными свойствами.
В результате получается долговечное, стойкое, высококачественное и привлекательное на вид покрытие с отличными защитными свойствами.
Упаковка и маркировка:
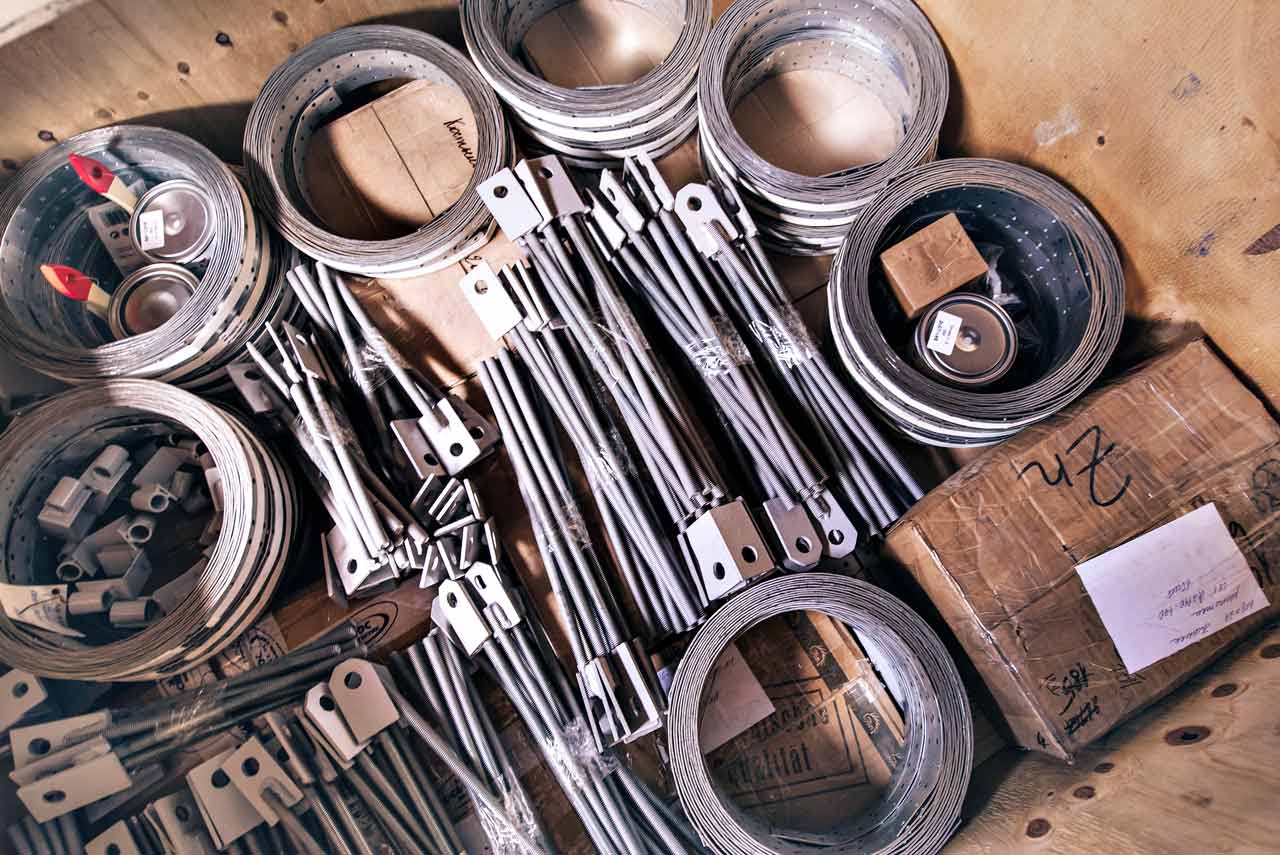
Маркировка наносится на все элементы металлокаркаса и секции тентового покрытия в соответствии с отгрузочной спецификацией.
Маркировку наносят способом, обеспечивающим четкое и ясное прочтение информации.
В качестве основного вида упаковки конструктивных элементов при транспортировании применяется пакетирование, при этом отдельные секции металлокаркаса прокладываются деревянными брусками и надежно стягиваются полиэстеровой упаковочной лентой.
Натяжение полиэстеровой ленты со временем не ослабевает, она нечувствительна к ультрафиолетовым излучениям и выдерживает высокие температуры, устойчива к атмосферному воздействию (не ржавеет и не оставляет на поверхности ржавых пятен), не повреждает декоративно-защитное покрытие.
Упаковка из укрывного армированного материала, применяемая для элементов тентовых покрытий исключает попадание влаги и внешних загрязнений. Дополнительно возможна упаковка в фанерные ящики.
Метизы, покупные изделия, детали крепежа поставляются фанерных ящиках, в упаковке предприятий-изготовителей.
Контроль качества:
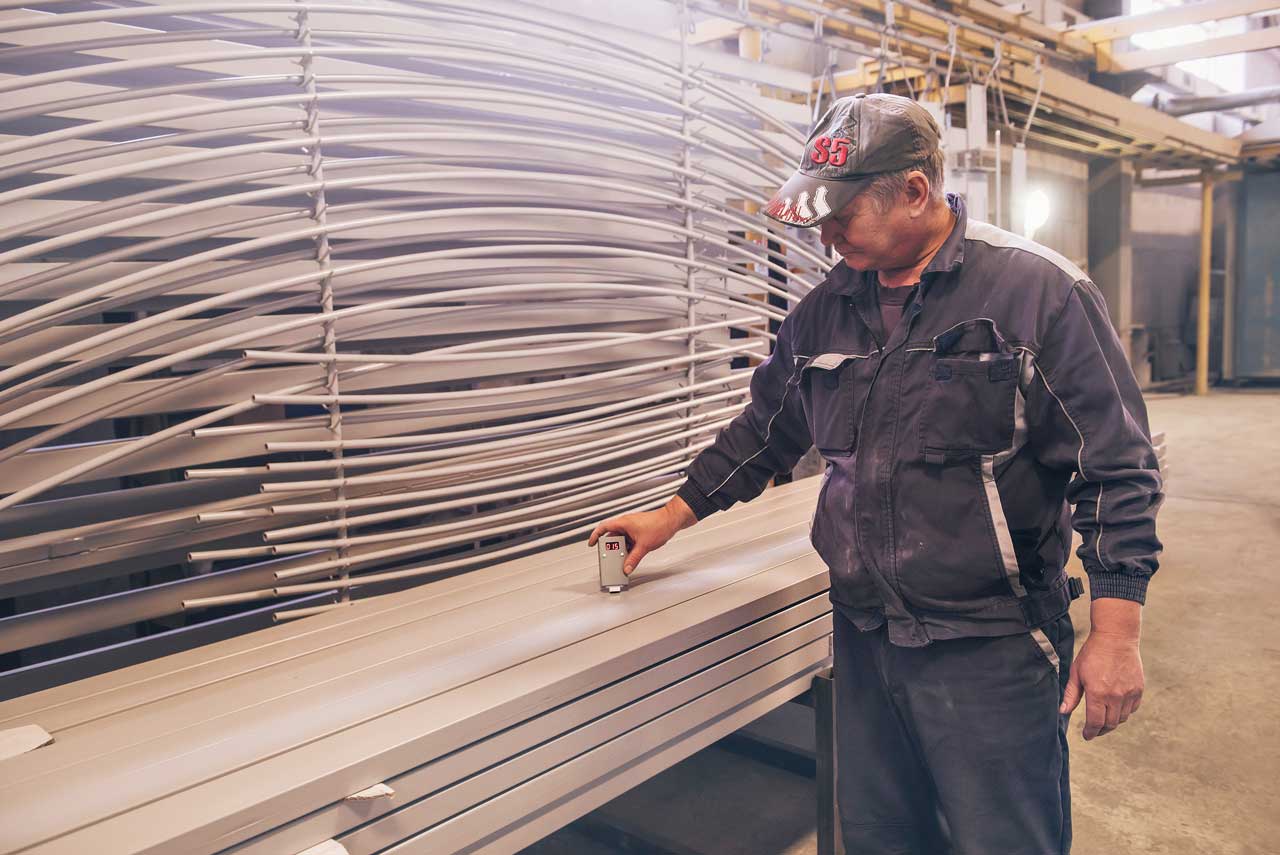
Все изделия изготовленные на нашем предприятии проходят приемку на соответствие требованиям ТУ, ГОСТ, СНиП, а также технического задания и прочих условий, указанных в технической документации и в договоре на изготовление сооружения.
Входной контроль:
Качество комплектующих изделий, исходных материалов, заготовок и покупных изделий.
Операционный контроль:
- – Сборка ферм и деталей конструкции металлокаркаса;
- – Качество сварных швов;
- – Геометрические параметры конструкций;
- – Качество антикоррозионных покрытий, в том числе подготовки поверхности.
Приёмо-сдаточный контроль:
- – Визуальный контроль конструкций;
- – Геометрические параметры конструкций, влияющие на собираемость конструкций;
- – Выборочный контроль сварных швов;
- – Комплектность, маркировка, упаковка.